Diamo una seconda vita alla plastica e salvaguardiamo l’ambiente
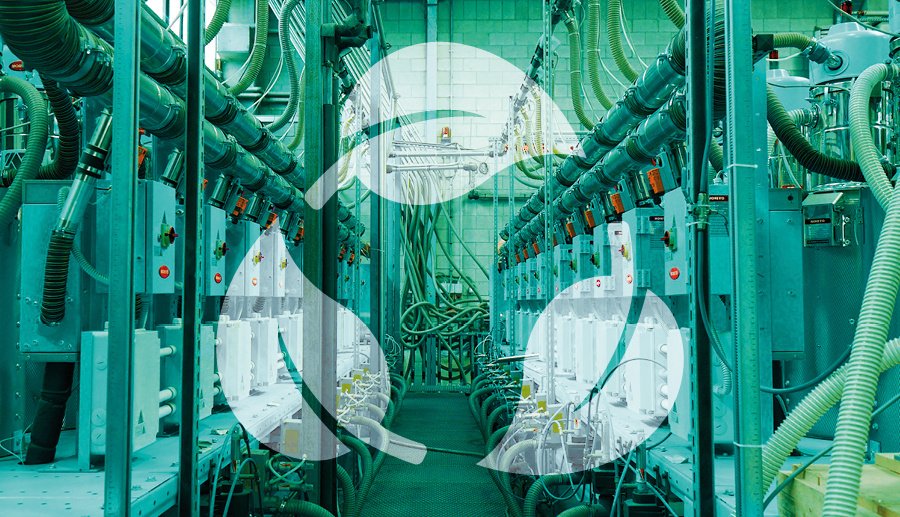
Un progetto di lungo periodo ha portato Techno ad adottare una serie di accorgimenti che coniugano l’efficienza industriale al rispetto dell’ambiente.
Nell’ultimo anno sono state gestite commesse per circa 134 tonnellate di materiale plastico: circa 44 di queste sono costituite da materozze e sfridi, per un’incidenza sul totale pari al 33.42%. L’implementazione di tecnologie all’avanguardia nel reparto di stampaggio e l’adozione di specifici accorgimenti ha permesso di recuperare la quasi totalità degli scarti di produzione e reimmetterli immediatamente nel ciclo produttivo.
Riciclo meccanico
Questo processo, che risulta di gran lunga il più sostenibile e a bassa emissione di CO₂, consiste nel rimodellamento degli scarti plastici di processo. Normalmente, le plastiche possono essere rimodellate tramite pressione e calore. Nel riciclo meccanico sono separate secondo specifici parametri come colore e tipo, dopodiché affrontano un processo di diverse fasi (fusione, filtraggio, estrusione) che termina con l’ottenimento dei granuli da reimmettere nel ciclo produttivo. Un’alternativa più ergonomica e sostenibile consiste nel mischiare la plastica vergine con quella riciclata: Techno ha scelto di adottare quest’ultimo processo a basso consumo energetico.
Nuovi criteri per gli stampi
In ottemperanza ai requisiti della ISO 14001, i nuovi stampi sono progettati per essere multi-impronta e con materozze di dimensioni minori; ove possibile, quelli già esistenti sono stati revisionati secondo gli stessi criteri, con il fine ultimo di bilanciare il rapporto tra prodotto finito e scarto e, in ottica più ampia, di ridurre l’impiego di materiali, i consumi di energia e le emissioni di CO2. Dunque, una revisione “a monte” in grado di rendere più agevoli le fasi successive del ciclo.
Plastica rigenerata in linea
Le presse a iniezione presenti nel reparto di stampaggio, sia quelle idrauliche inverter e che quelle full electric, sono state dotate di granulatori che rigenerano il materiale proveniente dalle materozze in plastica o dai pezzi scartati, secondo un processo completamente automatico e monitorabile da remoto. Tramite un tubo trasportatore, la plastica rigenerata viene convogliata nella pressa di stampaggio, senza alcuna movimentazione o intervento manuale, e utilizzata secondo i quantitativi prescritti nelle specifiche del prodotto da stampare.
Processo misto per plastica e gomma
I pezzi bicomponente che non superano il controllo di qualità in linea e gli scarti di avvio, affidato a sensori e robot, sono prelevati da un operatore e conferiti manualmente a un mulino granulatore collocato in un’area adiacente al reparto di stampaggio. Le materozze in gomma sono invece separate in linea da robot manipolatori e raccolte in contenitori; una volta riempiti, un operatore li conferisce nei macinatori presenti in un’apposita area dello stabilimento Techno. In prospettiva più ampia, il 70% del materiale è recuperato e rigenerato direttamente in linea, il restante 30% è recuperato da un operatore e immesso manualmente nei mulini granulatori e poi successivamente recuperato.
Quando si usa il materiale riciclato?
Techno ha stabilito specifici criteri relativi alle caratteristiche dei materiali da impiegare per ciascun prodotto. Per quelli di classe A, ossia dalle specifiche tecniche molto stringenti, e per i componenti in gomma, è prescritto l’impiego di materiale 100% vergine. Per altri componenti è previsto il materiale rigenerato, in una percentuale variabile a seconda delle specifiche tecniche validate dall’ufficio qualità di Techno.
La chiave di fissaggio è green
Da alcuni prodotti realizzati con PA66 e dotati di componenti in gomma deriva il materiale di seconda vita adatto a produrre la chiave di fissaggio presente in molti kit di connettori pronti all’uso attualmente in vendita. L’utensile è realizzato con un blend di tecnopolimeri – composto al 75% da PA66 autoestinguente rinforzata in fibra vetro, al 25% di PA66 autoestinguente non rinforzata - e gomma Post Industrial Recycle (PIR).
La portata degli interventi eseguiti
Considerando che l’incidenza media degli scarti è pari al 33% circa, oggi Techno ne recupera circa il 30% trasformandolo in materiale nuovamente utilizzabile; la restante parte viene affidata ad aziende specializzate nel recupero post consumer (PCR) o conferita in discarica.
Tradotto in quantitativi reali, il 97% del materiale pianificato dalle commesse Techno è trasformato dal processo, sia come materiale vergine sia come macinato / rigenerato.
Per il futuro, l’obiettivo è portare l’incidenza degli scarti non ri-utilizzabili alla soglia del 2%, nell’ottica di un miglioramento delle prestazioni industriali e di un ulteriore significativo passo in avanti in termini di sostenibilità del processo produttivo.